The importance of solid subfloor
Updated: 2022-01-13
By Paul Bianchina
As you walk across your living room carpet or stand on the vinyl flooring in your kitchen, you're probably completely unaware of the structural floor that lies beneath the finished flooring. Called the subfloor, this structural component of your home lies across the tops of the floor joists and offers lateral stability to the floor framing as well as a solid, flat floor surface.
As you walk across your living room carpet or stand on the vinyl flooring in your kitchen, you're probably completely unaware of the structural floor that lies beneath the finished flooring. Called the subfloor, this structural component of your home lies across the tops of the floor joists and offers lateral stability to the floor framing as well as a solid, flat floor surface.
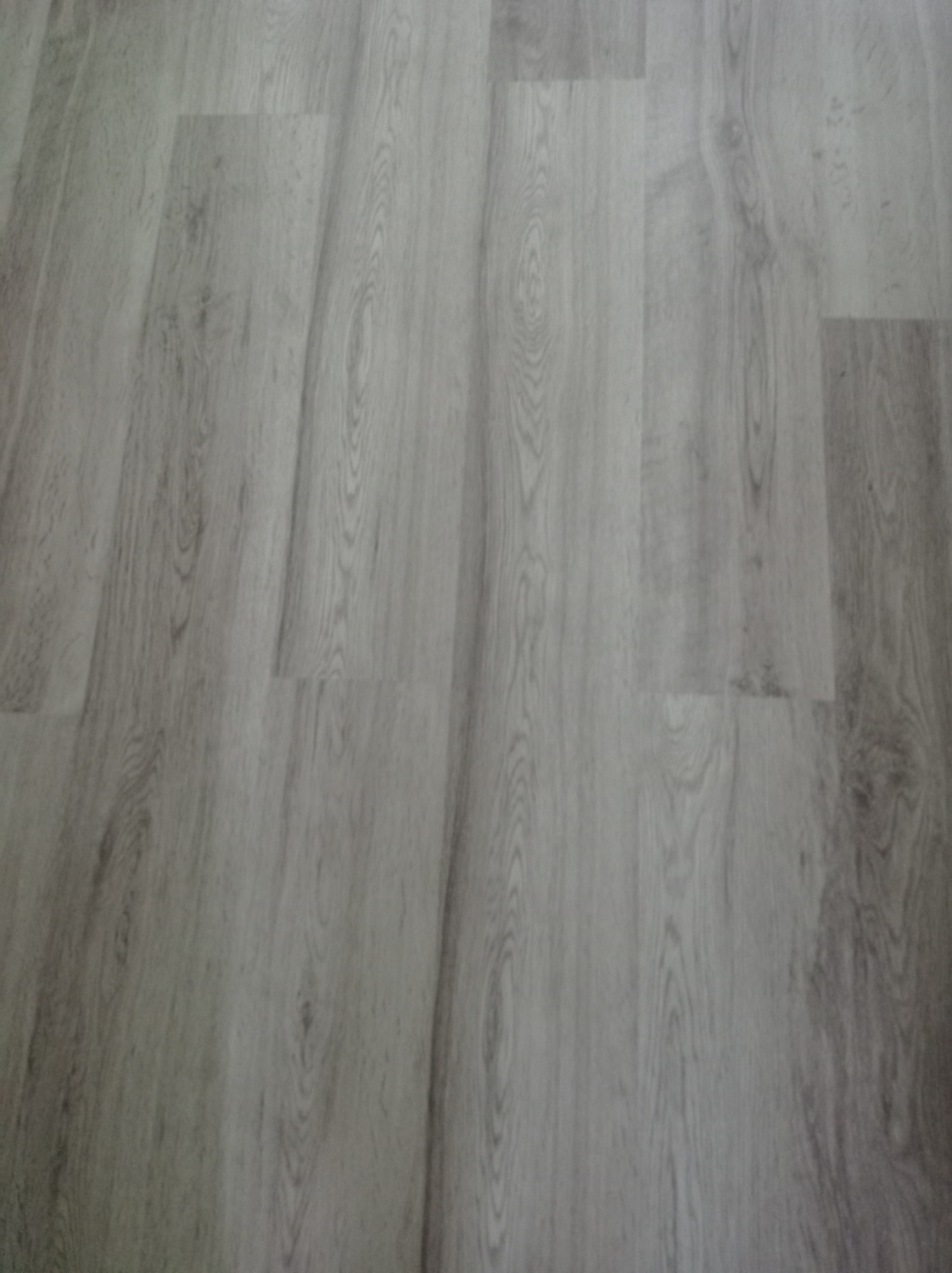
Proper selection, installation, and fastening of subfloors is essential to the structural integrity of the building and also to the comfort of the occupants. Improperly installed, subflooring can be bouncy and is apt to squeak, two very unpleasant attributes in a floor that should feel rock solid underfoot.
In years past, in the days before wall-to-wall carpeting, structural subfloors were typically installed by laying individual 1x planks diagonally across the tops of the joists. The planks were nailed in place without adhesive, and their diagonal installation helped brace the floor structure as well. A layer of felt or Kraft paper was installed next to block air from the crawlspace from coming up through the gaps between the boards, then finally the finished floor was installed. This was typically tongue and groove wood planks in most living areas, with ceramic tile, sheet linoleum or tile squares over an underlayment of plywood in kitchen and bath areas.
Diagonal installation was both time consuming and wasteful of materials, and as both labor and material costs rose, most builders switched to straight installation of 1x planks. Another popular subfloor was 2x6 or 2x8 tongue and groove boards, which could be installed over floor beams spaced up to 48 inches apart. Both methods, however, were still time consuming, and still required the installation of an air/moisture barrier and an underlayment material over the top to smooth out the subfloor prior to installation of the finished flooring.
The material of choice today - and for the last couple of decades -- is sheets of tongue and groove plywood or other composite materials. The 4-foot by 8-foot plywood sheets install quickly with less labor than planks; they offer excellent lateral bracing for the floor joists; they provide both a moisture and an air barrier between the subfloor and the crawlspace; and, perhaps best of all, they provide a smooth surface for the installation of most types of finished flooring.
Subfloor sheets are typically found in one of three basic materials. Plywood, comprised of wood veneers laid up in layers, with each layer perpendicular to the ones above and below it, is still one of the most popular subfloor choices. Composite plywood, under the trade name Com-Ply, is another popular choice, with a veneer layer on the top and bottom and a core of reconstituted wood. A third option that is growing in popularity is oriented strand board (OSB), which is comprised of thin layers of wood chips glued up under heat and pressure.
Sheet subflooring is typically installed by starting in one corner of the floor and laying a full sheet on top of the joists. The long axis of the sheet is installed perpendicular to the direction of the joists, and the groove side of the plywood is against the edge of floor structure, so that the tongue faces out. The second sheet is butted to the end of the first one, so that the ends of both sheets fall over the center of a floor joist.
The second row of subfloor begins with a sheet that has been cut in half, so that it is 4 feet by 4 feet. The sheet is set on the joists so that the end is even with the end of the first sheet in the first row, then the new sheet is slid back towards the first sheet, allowing the groove to interlock with tongue of the other sheet. Starting the second row with a half sheet and then continuing the row with full sheets creates a staggered installation, so that the ends of the sheets in each row fall over the center of the sheet in the row preceding it.
Subfloor sheets are installed using a compatible subfloor adhesive that is available in tubes for use with a caulking gun. A bead of adhesive is spread on top of the joists, then the sheet is lowered down onto the adhesive. The sheet is then fastened using ring-shank nails, screws, or staples. Common fastener spacing is 6 inches apart along the edges of the sheets and 12 inches apart in the field.
Installation methods and materials can vary between the different types and thicknesses of sheets being installed, so be sure and ask your lumber dealer for specific instructions
Comments (0)