Concrete Placing
Updated: 2021-10-23
Article by Bill Bradley
Concrete placing is the process of getting the concrete, from the mixer, whether it be on a transit mixer truck or a concrete mixer on site, and into the formwork and screeded off level. This will leave you ready for applying the finish.
Before we even get to that though, you should have already done your preparation work.
If you are laying concrete on the ground, say for a driveway, like the guys in the photographs I am using to illustrate this topic, you should have already done the following :-
There are a couple of other jobs too, that should be done before the concrete arrives.
Concrete Placing. These guys started at the bottom of the slope working uphill. Note the height of the chute and the consistency of the concrete. Another guy is tapping the forms with a hammer, now and again he heaves up n the mesh if it is sagging.
OK, so we are all ready to go, nice and early in the morning. All the preparation work has been done the previous day, to avoid any unnecessary delay when the truck arrives. The correct mix has just arrived in a transit mixer truck.
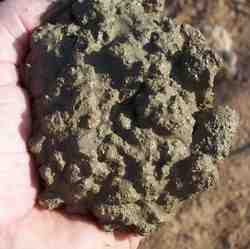
Concrete placing is the process of getting the concrete, from the mixer, whether it be on a transit mixer truck or a concrete mixer on site, and into the formwork and screeded off level. This will leave you ready for applying the finish.
Before we even get to that though, you should have already done your preparation work.
If you are laying concrete on the ground, say for a driveway, like the guys in the photographs I am using to illustrate this topic, you should have already done the following :-
- Remove vegetable matter. I am not talking about market gardening here, I just mean that top layer that contains grass, loamy soil, mulch or weeds and other crap. Get down to subsoil. By hand or with a machine ( "Bobcat" or similar skid steer loader). Cut out tree roots and so on.
- Compaction. If you then have to add fill to get the correct levels, make sure that it is compacted. This could be as simple as watered sand or sand or gravel fill compacted with a machine, say a plate compactor.
- Formwork. You will need formwork of some sort to contain the concrete, to define the edges. On small jobs like shown here, it also is a guide for the top of the concrete.
- Vapour barrier. I like to see a plastic membrane laid under the concrete. On house slabs it is mandatory, to stop dampness rising through the concrete slab, but for driveways it is optional, and so you don't have to do it, but using a membrane underlay stops the plastic concrete (that's concrete that is still in a wet, manageable state) from drying out too quickly or unevenly. If you pour concrete onto dry earth, a percentage of the water in the concrete will soak into the soil, so changing your precious water cement ratio. At the very least if you are not using a vapour barrier, water the earth down to stop too much water being sucked out of the concrete.
- You will need your rebar or reinforcing mesh in place, if it is needed. Packed up to the correct height with bar chairs.
There are a couple of other jobs too, that should be done before the concrete arrives.
- Tidy up the site, things get a bit intense when pouring concrete, so do yourself and your mates a favour and shift the crap from out of your way.
- If you are using wheelbarrows, pump up the tyres. If you are a first time concretor, make sure you have a decent solid wheelbarrow. Garden barrows just won't handle the loads.
- Make sure the tools etc. that you need are on site and good to go. Fuel up vibrators etc.
Placing the concrete
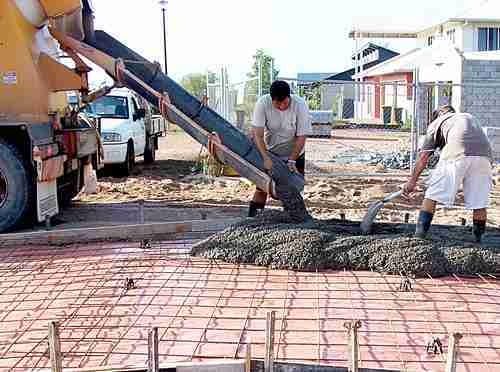
Concrete Placing. These guys started at the bottom of the slope working uphill. Note the height of the chute and the consistency of the concrete. Another guy is tapping the forms with a hammer, now and again he heaves up n the mesh if it is sagging.
OK, so we are all ready to go, nice and early in the morning. All the preparation work has been done the previous day, to avoid any unnecessary delay when the truck arrives. The correct mix has just arrived in a transit mixer truck.
- The concrete that arrives at the job will normally be as good as it gets. You can of course stuff it up, by adding extra water, and I have already said that adding extra water is equivalent to throwing $50 bills into it. There are exceptions of course, where conditions change, like you have underestimated the time it will take you to place the concrete, but on a well organised job there is no reason to add extra water.
- Segregation. You can stuff up a good mix in another way too. That is allowing the concrete to segregate into it's component parts.
- Concrete should not be allowed to fall freely more than a meter or so.
- You are pouring a basement floor, you must not just dump the concrete in there. Either provide extra chutes or hire a pump.
- Pouring concrete stairs, start at the bottom and place the fresh concrete on top of the already placed stuff. Don't let it slide downhill.
- The reason that the transit mixer always has the bowl slowly turning is to keep the correct consistency of the concrete.
- Transporting wet concrete over a distance, say in the bucket of a loader, or in a trailer, just does not work. What happens is that the heavy solids gravitate to the bottom, the lighter sand and cement is in the middle and the water is on the top. So much so that it becomes almost impossible to dig out with a shovel. This is concrete segregation at it's worst.
- So, back to our normal job, Start at the low end. Work uphill.
- Keep the chute low and close to the placed concrete. Try not to drop it or drag it too far.
- Place fresh concrete up to the older concrete.
- Keep one face working at a time, that is don't do odd patches here and there.
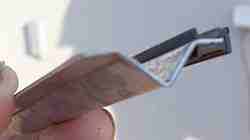
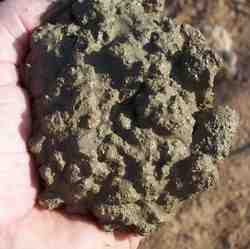
Concrete Placing - Left pressed metal control joint with rubber cap. Right, a hand full of the first concrete out of the chute. Experienced concretors get a feel for the concrete and can tell by the look and feel if it is a good mix. This is a 10mm paving mix that will have an exposed aggregate finish.
Compaction
Another way to devalue the quality of your concrete that you have forked out good cash for, is to not compact it correctly. Concrete when mixed in the bowl of the mixer entraps a certain amount of air.
In the process of getting it out of the truck and into position on the job, there is inevitably a certain amount of more air trapped in the mix. Apart from some special concrete mixes, this air is not wanted. We remove the air, to compact the mix back to it's basic ingredients by vibration. This liquefies the mix and allows the air bubbles to rise to the surface.
In the process of getting it out of the truck and into position on the job, there is inevitably a certain amount of more air trapped in the mix. Apart from some special concrete mixes, this air is not wanted. We remove the air, to compact the mix back to it's basic ingredients by vibration. This liquefies the mix and allows the air bubbles to rise to the surface.
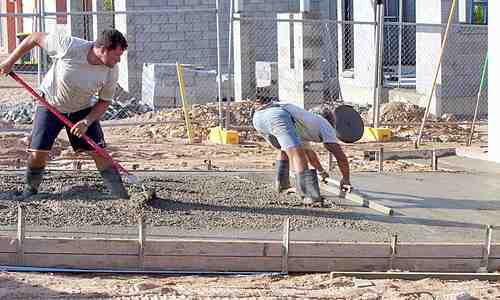
Concrete Placing - This guy works around the outer edge with a 3M. long aluminium screed, (he has a selection of different screeds) leveling a strip about 400mm wide to work from, using the top of the formwork as his guide. He then uses those strips as guides, to screed off the main area He does not actually screed off the top of the forms. His offsider works with him leveling and raking away the excess.
- For the job pictured, a 100 thick driveway, the vibration was done by hand.
- From time to time as the pour progressed one of the guys would grab a hammer and tap the formwork, setting up a vibration along the timber form. When this is done, you can actually see bubbles rising to the surface. Apart from the quality of the concrete aspect of this, there is also a visual aspect. If you don't do it, you get unsightly air holes on the edge of the concrete when the formwork is stripped.
- When the concrete is being placed and levelled the guys on the shovel and the rake work the mix up and down to compact it.
- The guy on the screed again tamps the surface up and down, as he starts levelling it.
- On thin slabs on the ground that are more critical than a residential driveway, like road surfaces or tilt slab panels, it is common to use large powered mechanical screeds that vibrate the surface and the edge forms consistently.
- For deeper concrete, like in foundations or walls it is essential to use a powered vibrator. Then the concrete is vibrated on the inside, rather than external vibration mentioned before.
- These consist of a motor driving a flexible shaft with a steel vibrator head on it. Commonly called pokers.
- They range from small 20mm or 25mm models, electric motor driven, to the normal 30mm petrol engined machine. Larger models still are compressed air driven.
Control Joints
We have to have joints in concrete. They are there to stop random cracking. As concrete dries out it shrinks, so it will crack. Joints weaken the concrete in places we choose, and so the concrete cracks where we want it to crack and not randomly. On the driveway job pictured the boys used a few different types of joints.
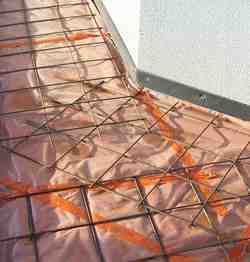
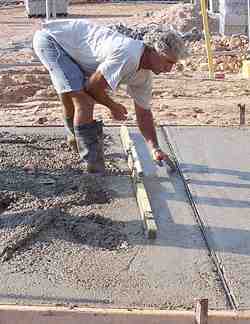
Concrete Placing - Left, a foam isolation joint fixed to the plastered surface of the house slab/wall. Fixed with masonry nails. The mesh will be lifted by hand as the concrete is poured. Right, laying a metal control joint into the freshly screeded concrete.
- A 12mm thick by 100mm deep bitumen impregnated foam strip, around the whole perimeter of the existing house slab, where the new concrete paths abut it. This material is commonly called an expansion joint. Or in this case it is used as an isolation joint That is, it separates two distinct parts of the building, and allows each them to move without affecting the other.
- At the end of a days work just a plain butt joint. On more critical jobs, key joints are sometimes used.
- Every 4M. or 5M. in the driveway, and say every 1.5M. in the footpath, a metal strip about 35 deep with a rubber cap is set into the wet concrete.
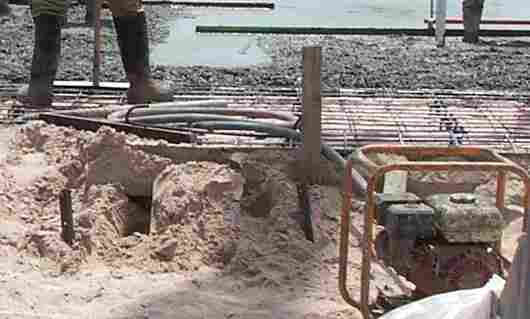
Concrete Placing - Petrol engine (bottom right) with 1 1/4 flexible shaft, with vibrator head. This will be used when the concrete from the 100 deep slab reaches the deeper edge thickening beams.
Bill has his own building related website.
Comments (0)